Episode 1
“What is Engineering?”
by Manabu Nakatani + Nanae Takahashi
(Design Engineers)
Manufacturing at A-POC ABLE ISSEY MIYAKE is led by the Engineering Team. It is not pattern, textile, or design, but “engineering.” The terminology is unique and idiosyncratic, as are the methods and concepts. The results take final form as products and projects. This time, key members of the team spoke about their work.
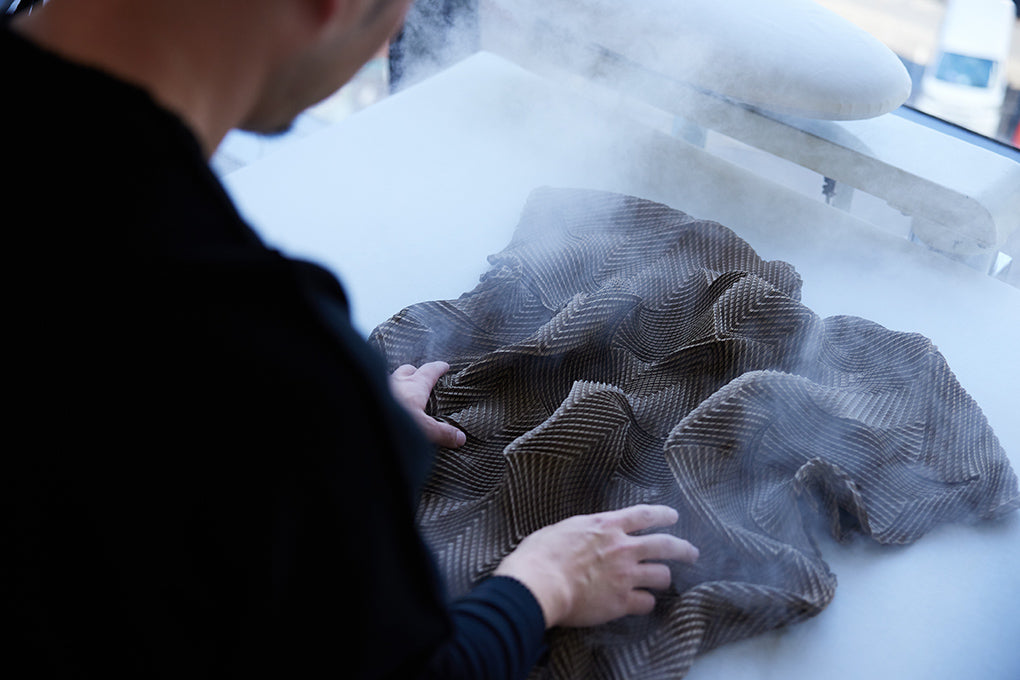
What is “engineering?”. Dictionaries probably say something like: “Engineering is the use of scientific principles in the research and work that goes into designing and building bridges, roads, vehicles, buildings, and other machines, structures and objects.” This seems far from what is commonly understood as the process of making clothes.
Nonetheless, or maybe precisely because of that, it is the Engineering Team that drives the manufacturing at A-POC ABLE ISSEY MIYAKE (“A-POC ABLE” below). Implementing the concept of innovation in each aspect of the manufacturing process requires there to be certain methods and structures in place, together with new ideas that have never previously existed. We discussed the background behind this in the first episode of DIALOGUES (Episode 0 “What is A-POC Thinking?”).
In this dialogue, we try to arrive at a more concrete picture of the relationship between “engineering and manufacturing.” Joining us for the discussion are Manabu Nakatani and Nanae Takahashi, design engineers who lead A-POC ABLE manufacturing. The key point seems to be the ability to move freely between different fields like textiles, patternmaking and design to formulate and develop new ideas. From there, the implementation process is structured and built. That is why the definition of “engineering” is the proper description.
──Our topic for this dialogue is how this “engineering” actually happens. In the previous dialogue, we looked at the question “why” and how it is a driving force in manufacturing. This dialogue starts by asking for more details on that point.
Manabu Nakatani (“Nakatani” below): When you are involved in design and manufacturing, you are confronted with issues and challenges. Miyake (Issey) constantly asked “why” anytime something happened, and as I look back on it, I realize that he was asking us to proactively think about how we personally would address the problems.
I joined Issey Miyake on the technology (patternmaking) side and researched solutions that involved shapes and lines, but there was no reason to stop there. You can also approach issues in terms of textiles and processing, and the more things you are interested in, the more options you have. More options in turn give you more flexibility when you are dealing with patterns.
──So you are not the kind of person who normally asks “why?”
Nakatani: That might be true. I sometimes allow myself to be carried away by the impulse of simply wanting to create clothing. I think people realized that about me. Not just Miyake, but all of the senior employees would ask “why” so often, I would get sick of it. I needed more than just options to answer that question; I had to fully understand what my objectives and methods were in creating each item of clothing.
When someone tells you “do this,” it is crucial that you be able to ask yourself “why am I doing this?” If you just do what you’re told, you do not gain any new perspectives or opinions. That is why the question of “why” is the driving force in manufacturing.
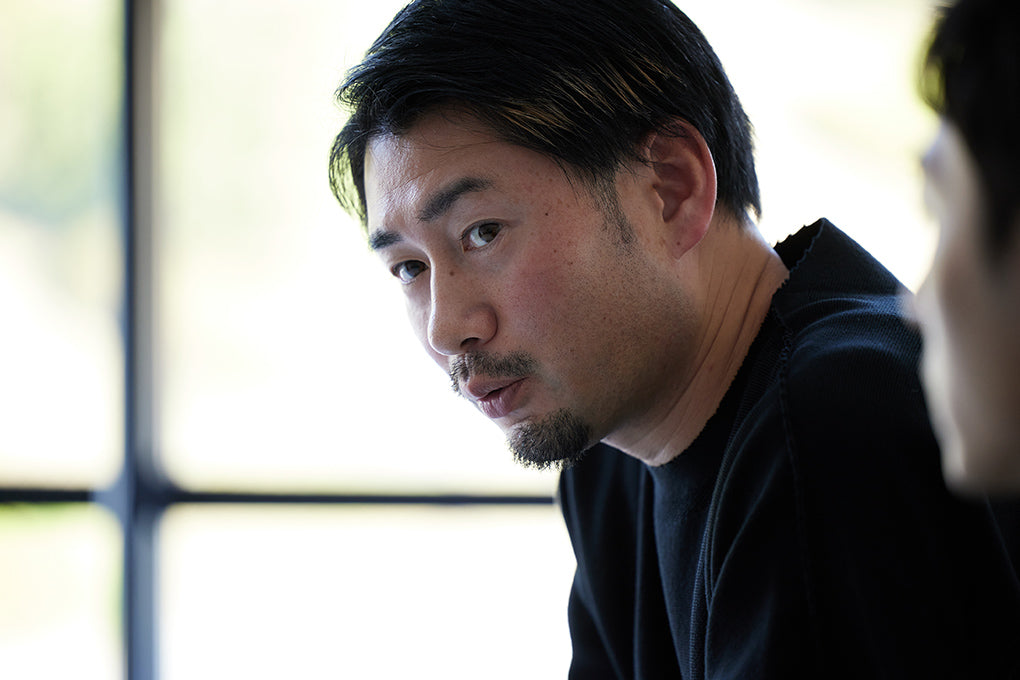
(Manabu Nakatani, Design Engineer, A-POC ABLE ISSEY MIYAKE)
──Takahashi-san, how do you deal with the question of “why?”
Nanae Takahashi (“Takahashi” below): I’m the opposite of Nakatani-san. I was first assigned to PLEATS PLEASE ISSEY MIYAKE, so there were already lots of whys for me: “Why do we need to use the shitsuke*process on garments prior to pleating?” “Why is it necessary to insert paper during the pleating process?” I had all sorts of questions about the manufacturing process right in the beginning.
My technical challenge from the start was to figure out how to eliminate the shitsuke basting from the manufacturing process. I was reassigned to another division two and a half years after I joined, so I never solved that problem.
──One of the unique things about A-POC ABLE is that its manufacturing is led by two design engineers with such different personalities. What is the appeal of crossing over into different fields as part of manufacturing, rather than dividing operations into textiles, designs, and patterns?
Takahashi: Depending on the brand’s expectations and vision, the conventional divisions of labor may sometimes be more suitable. But at A-POC ABLE, we can tell an entire story from a piece of cloth, or if necessary, a single thread.
If all you can do is patternmaking, you will frequently be stopped in your tracks as you wonder why this particular fabric is used for this particular design. It’s like wondering whether the ingredients really match the recipe. With patternmaking alone, there is a certain residual irritation because you can’t solve all the problems.
Nakatani: Obviously, when you first join Issey Miyake, it may be difficult to have the same kinds of questions that Takahashi-san had, like “is it even possible to create this shape with this fabric?” But you begin to become aware of these sorts of things if you continue to ask yourself “why” in the process of gaining experience. And then you no longer only have questions, but also proposals: we can use this method to create the desired shape, or maybe this shape would be better, or maybe we should use this material instead.
It goes without saying that you need to have learned quite a lot before you can start talking about materials. You can use exactly the same thread to create vastly different fabrics depending on the weave and density, so it is difficult to have meaningful conversations with the textiles specialists if you lack experience. That being said, once textiles become a potential option for you, there are all sorts of possibilities.
There is vastly more freedom and enjoyment in creating clothing when you’ve built up a certain amount of experience and knowledge in different fields and are able to think about them on your own. You are also able to consider the wider impact on shops and business.
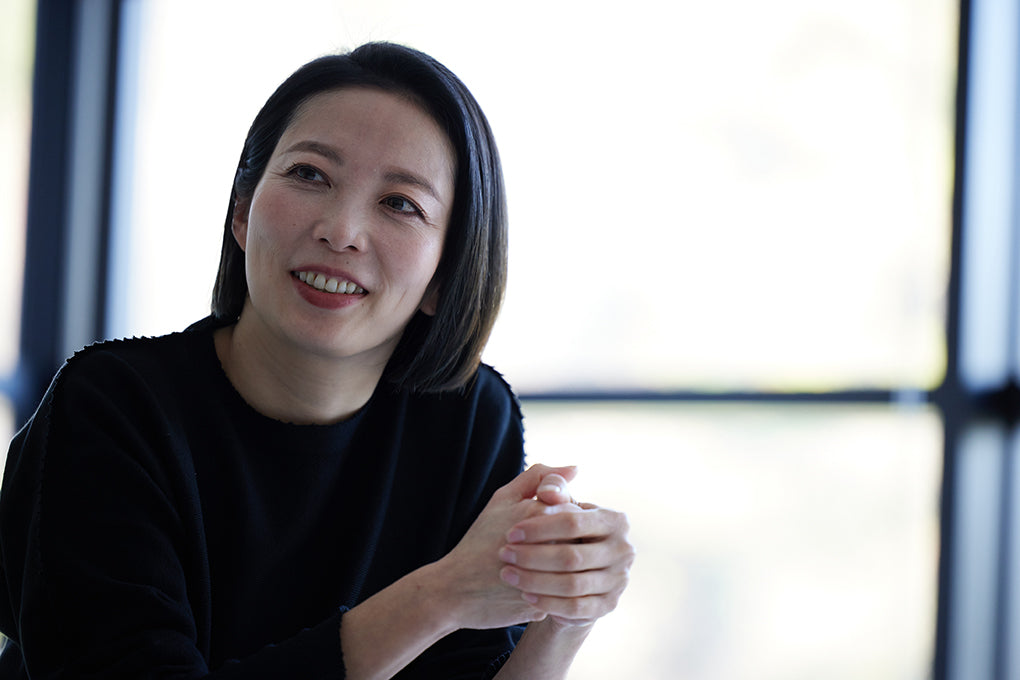
(Nanae Takahashi, Design Engineer, A-POC ABLE ISSEY MIYAKE)
──In other words, you’re able to look at the big picture in manufacturing. That is one of the benefits of engineering at A-POC ABLE.
Takahashi: That’s true. The things that you learn through technical work do not end just with technology, but continue on into design and textiles. I think you can do more interesting things when you are able to explore these fields. The word “engineering” seems a bit industrial, which is a slightly different nuance from making clothes.
Nakatani: That’s right. But sometimes we do things that are very similar to industrial engineering and structural design. Takahashi-san talked a moment ago about wanting to eliminate the shitsuke basting, and an important question is how to advance and upgrade the manufacturing process without losing quality. For example, you ask yourself if there is some way to simplify the sewing, or if you can boost efficiency by incorporating information about seam allowances into the fabric. It’s incredibly fun and rewarding to be able to consider and then implement these ideas.
──Your perspective expands to the manufacturing process behind the apparel, something that is not apparent on the surface.
Nakatani: That’s true. When there are already rails in place, you can continue down them, but for us, part of the manufacturing job is to lay new rails where none exist. That is easier said than done. It is not a simple job, but that makes it all the more rewarding and all the more gratifying when your ideas finally take shape.
It’s not so much finding your own manufacturing as it is building an environment for manufacturing and exploring new possibilities. This is something we place a lot of value on at A-POC ABLE. I don’t think we would be able to create our clothing if we didn’t value this.
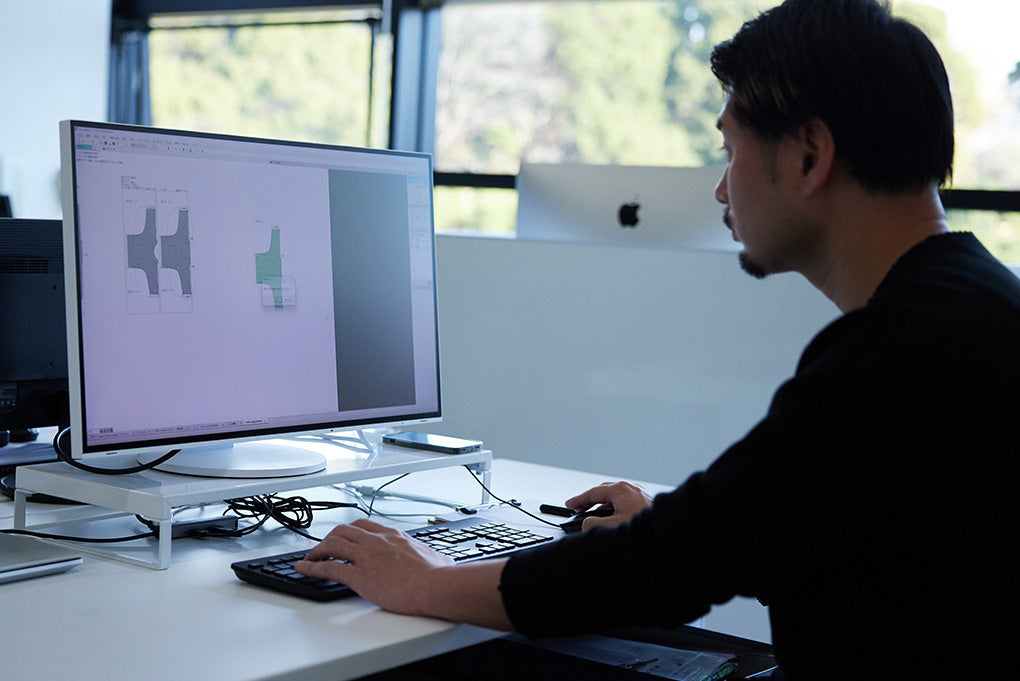
──I think I have come to understand what the brand’s concept of “revolutionizing the process of cloth making” represents.
Nakatani: The people at the factories and the craftsmen are all part of our manufacturing team. We are searching for and exploring new methods that have never before existed, and it doesn’t always go smoothly from the start. Nonetheless, we are able to discuss things, and sometimes argue about them, honestly and forthrightly, and in the process, begin to understand each other better. Today, we have specialists in Japan that focus on different aspects like sewing and processing.
──What do you emphasize as you create these environments?
Nakatani: I think it’s important to not be overly strict about rules. You can articulate a clear goal (this is what I want to make) and then to a certain extent present processes and recipes to achieve it. But beyond that, you try to leave things up to the people at the factory. Obviously, when problems are encountered, you need to reconsider and propose something different, and if there are easier or more efficient approaches, you need to allow people to make changes. The conventional approach is to draft an instruction statement that says, “Do it this way.” But if you become too focused on that, you stop thinking and put a lid on new possibilities.
──It’s not a question of neglecting your responsibilities or leaving everything up to someone else, but rather building a relationship in which everyone is able to act independently. I consider it a very effective method for expanding the potential for manufacturing, but it is certainly not easy to build this type of team.
Nakatani: I don’t know if this is much of an answer, but when I want to start making something, I immediately first see in my mind the faces of the people at the factory who will be responsible for the production. I ask myself how to make it easier for them, “how can we make it easier to sew” and “would it be easier to apply steam if we did it this way.” This then becomes a program that can be incorporated into the fabric as the product takes shape.
That is something you can only do when your viewpoint has expanded beyond patterns to the processes by which the fabric is created, sewn and processed. If you are simply making things, maybe you don’t need to pay as much attention to whether the product is easy to sew or mass-produce. But we do not countenance the attitude of “somebody else will take care of the rest.” As much as possible, we want to build the manufacturing process into “a piece of cloth.” This makes it very gratifying when you find, for example, a way to make the sewing easier without compromising the comfort or value of the product.
Takahashi: I agree. I think that’s why I wanted to eliminate the shitsuke basting. I also think that we need time to build relationships not just with the factories but also, for example, with the traditional dyers, and the people who want to engage in the same kind of manufacturing as we do.
It’s difficult to ask someone to do something different from what they’ve done before if they are part of a long tradition or if they are skilled, experienced craftspeople. But we want to explore new possibilities. This leads to us spending several years, sometimes six or seven, visiting workshops and building up our mutual understanding of the work. As this relationship grows, we become a team that can work together to take on challenges.

Nakatani: We want to do more of this. We want to see the future that lies at the end of the process. That means thinking not just about what you want to make right now, but how and with whom you want to make it, and what new potentials will emerge because of that. If you use the same machinery to do the same thing, you will get the same product. But we want to work with plants and craftsmen to explore, little by little, new methods. Part of our job is to create the optimum environments and build the relationships to achieve that.
──It’s not just about creating new products, but through that process, expanding what it is we are able to do. I have a much more concrete idea about engineering at A-POC ABLE. You need to expand your range and increase your options to be able to do this, right?
Nakatani: This may sound paradoxical, but the more options you have, the better you are at subtracting ideas. I think it’s wonderful to use an additive approach where you create new value, but there is also an attraction to high quality that is both simple and refined. You can think about the kinds of situations in which different kinds of customers would want to wear this particular piece of clothing, and that allows you to develop a purer program to achieve your objectives.
If you are able to think like that, then you avoid the pitfalls of making things for the sake of making things. “You are able to design even the expressions of joy on your customers’ faces.” That was something that Miyake said, and I’ve been thinking about it a lot lately. If you are able to imagine the face of the wearer and understand what they are feeling as you create the clothing, you are better able to engage in the manufacturing process with much more accuracy. That is extraordinarily rewarding.
Takahashi: I understand what you are saying about the subtractive approach and how interesting it is. Simplicity is an important factor in generating new interest and encouraging people to wear your clothing. Strangely, the simpler A-POC ABLE clothing becomes, the clearer you are able to see the manufacturing process and the Miyake philosophy behind it. I think clothing can represent an opportunity or a trigger for someone. Engineering brings opportunities both to the people who wear the clothes and the people who make them.
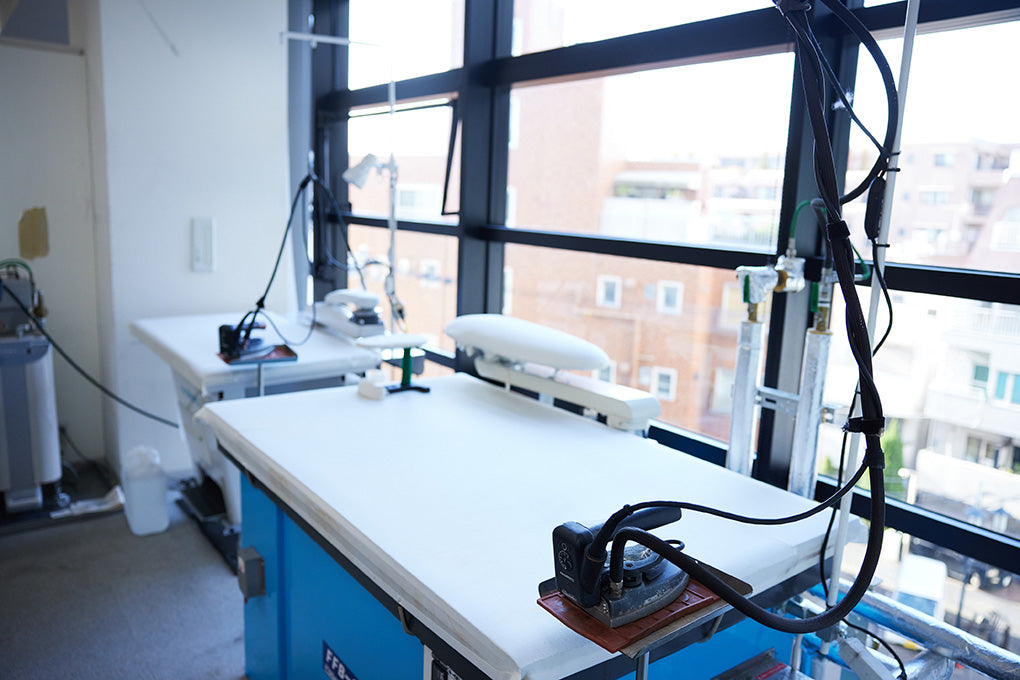
*“Shitsuke” is unique to Japan and refers to the process of stitching to secure folds when tailoring a kimono, typically applied to sleeves and other areas. In the context of PLEATS PLEASE ISSEY MIYAKE, it refers to stitching threads to ensure that the fabrics in the front and back of pre-sewn garments remain aligned when pleating on the pleats machine.
Stay tuned for Episode 2, where we will be discussing “Freeform Design”.