Episode 0
“What is A-POC Thinking?”
by Yoshiyuki Miyamae (Designer) + Engineering Team
Passion and curiosity for innovative creations drive the engineering team at A-POC ABLE ISSEY MIYAKE. Whether it’s exploring a single thread, reexamining methods for continuous improvement, or meticulously researching new ideas, all these endeavors may be seen as reflections of our ethos. “A-POC” stands for “A Piece Of Cloth,” representing a simple yet profound inquiry that is inherent to the essence of this team.
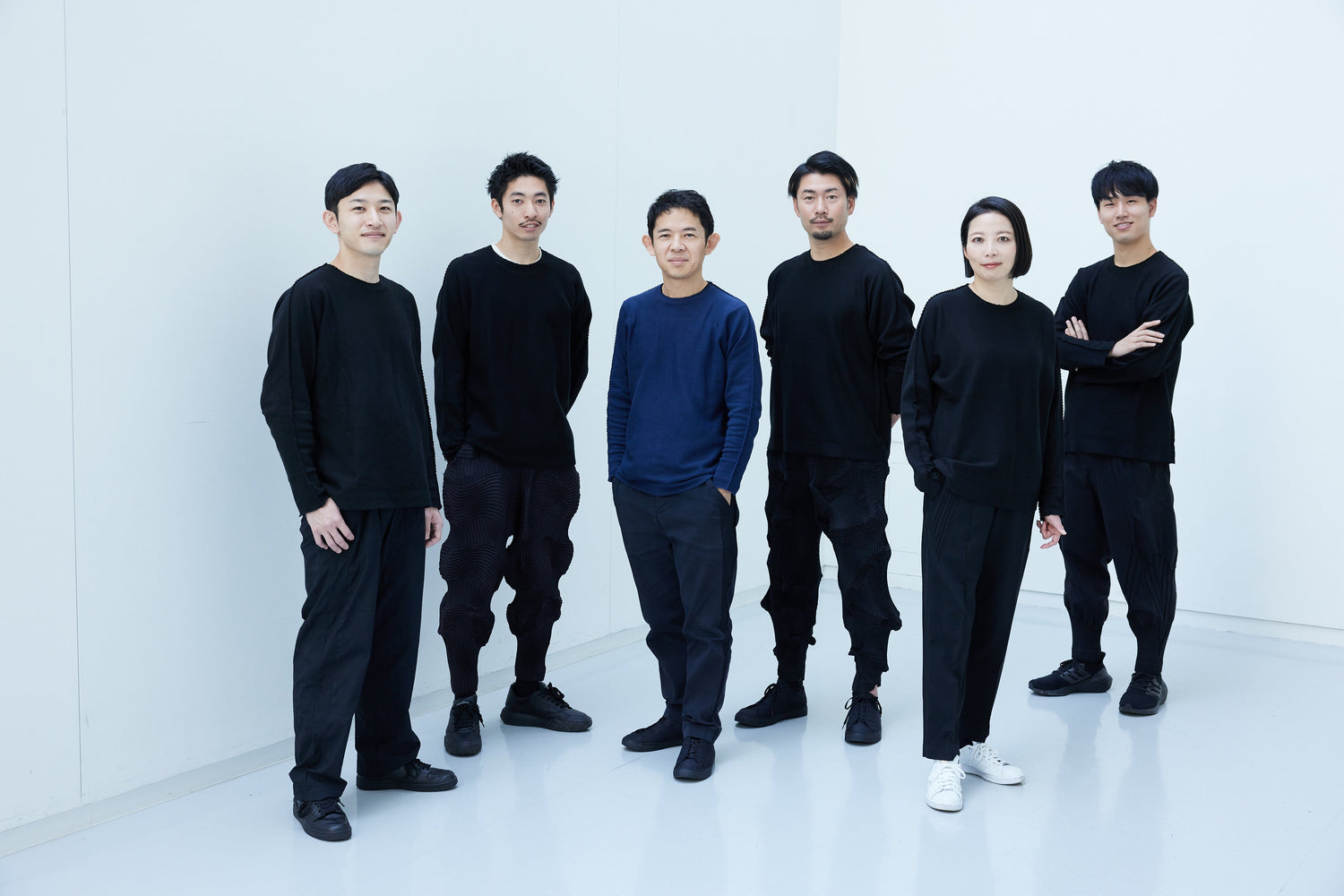
(The Engineering Team at A-POC ABLE ISSEY MIYAKE, led by Yoshiyuki Miyamae)
The Engineering Team is responsible for the design and making at A-POC ABLE ISSEY MIYAKE (“A-POC ABLE” below). General practice in the industry is for people with expertise in design, textiles, patternmaking and other areas to divide up responsibilities for clothing creation, but for this team, the approach is usually for the entire team to have sole discretion over the garment making process,from the initial conceptualization and planning, including research and development of materials, decisions on form and details, to the preparations for mass production.
This unique A-POC ABLE design structure was created by designer Yoshiyuki Miyamae as he searched for a new way of manufacturing. The idea emerged from the “A-POC” concept first conceived by Issey Miyake in 1998. A-POC was Miyake’s vision for clothing in the 21st century, and was inspired by the idea of “revolutionizing the process of design and manufacturing to create a new approach in which the wearer would also be a participant in the design.” This informed many of the new clothing concepts and experimental creations that were to come. We spoke with Miyamae and the Engineering Team about the intentions and ideas behind A-POC ABLE, how they were developed, and the collections they are producing.
- Why was an engineering team organized for the purpose of creation?
Yoshiyuki Miyamae (“Miyamae” below): Indeed, the term “engineering” isn’t commonly heard in the fashion industry. Even within Issey Miyake, the creation process is typically divided into three sections: design, pattern-making, and textiles. However, when it comes to the work of A-POC ABLE, we felt the need for a unique team structure to approach creation in a novel way.
Our mission is not merely to make clothes but to scrutinize and revolutionize the entire process of creation. While this approach may seem unconventional, we feel there are limitations to thinking within existing frameworks. Without being confined to specific fields, each member must acquire specialized skills and knowledge to transform the process itself. Therefore, our work is not solely design or pattern-making; it is engineering.
The A-POC ABLE Engineering Team is led by Manabu Nakatani and Nanae Takashi, who both started their careers in technology however, through their work on A-POC ABLE, have now extended their research into areas like materials and processing. In an ordinary design studio, that would be the job of the textiles unit, but that is not the case in A-POC ABLE. Product development in the Engineering Team is a collaboration between design and engineering to investigate and research materials and create the final patterns.
- The normal process would be to have a designer sketch and pick the fabric, and then a patternmaker would give it form. This is different.
Miyamae: That’s right. Like planning (design), it requires quite the capacity to manage the entire process. We don't just think about style and image, but we start by developing materials and incorporating all of the elements required for the design into a piece of cloth. For example, we develop the patterns and the functions that the clothing will have upfront. You have to span all of these different areas before you can even begin to create A-POC ABLE clothing.
Of course, people are at different stages in their careers, and not everyone on the team can do everything. Nonetheless, what we want to achieve in engineering is something that goes beyond individual areas of expertise. We want to change the existing manufacturing process by using our individual knowledge, experiences and aesthetic sensibilities to freely research and discuss new ideas. This may appear to be a convoluted process, but we think it is the most direct way to explore new potentials for new apparel.
- Nakatani, you previously spoke about how your skills started to rapidly expand as you were working on A-POC ABLE.
Manabu Nakatani (“Nakatani” below): I was interested in the structure of clothing, and my work in apparel design and manufacturing at Issey Miyake has been an effort to satisfy, day in and day out, my curiosity in this realm. Obviously, patterns are an important part of clothing structure, but even before I became involved in A-POC ABLE, my attention had naturally been drawn to fabrics and thread. The major challenge was how to use unique, individual perceptions and ways of thinking to create new forms. I think a key factor was that this is an environment where you are free to pursue whatever interests and intrigues you regardless of your field of specialty.
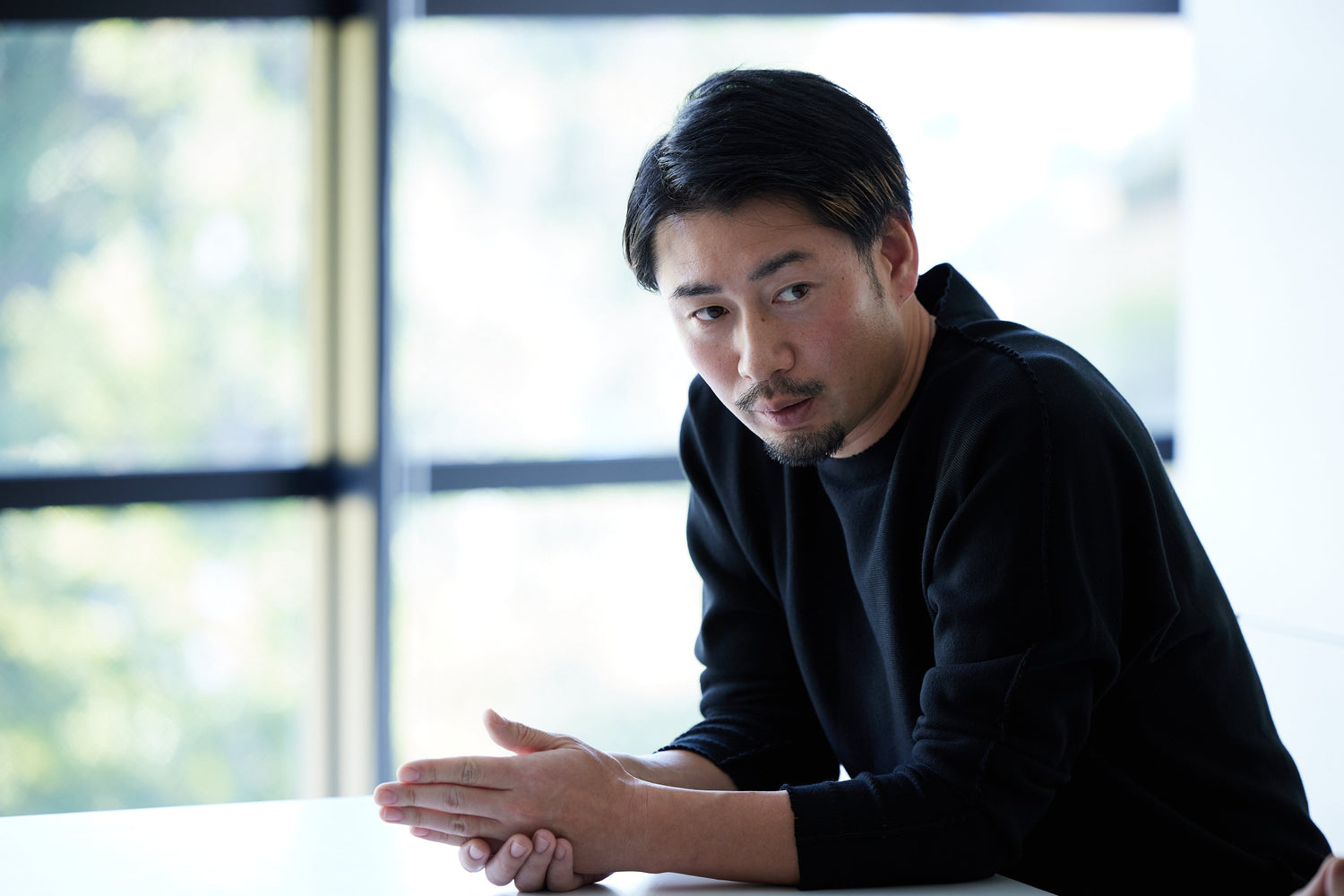
- So were you always more interested in the engineering side?
Nakatani: When I first joined the company, Miyake would constantly ask, “Why?” “Why do you think that?” “Why this line?” “Why this approach?” His questions went beyond just patterns and sewing. He wanted to know about how people would feel wearing the garment in their daily lives, about how it would function in society. This only further stimulated my curiosity because I realized that I needed to formulate these questions and find the answers on my own.
At the time, it felt like a natural process of growth and development, but as I look back on it, I think I gained something very special. In our world today, you can instantaneously access information over the Internet, and that information is indeed important, but it is also important to act, to use your hands and develop your own process. It is only when you, on your own, have identified a challenge that you really start to think deeply and seriously. That habit of continuing to ponder and think may be the reason why I am where I am today.
- Takahashi, were you also asked “why?”
Nanae Takahashi (“Takahashi” below): I always liked clothing and fashion, and at the time I decided to become a designer and patternmaker, I realized that I was headed in a very unusual direction. Most people who say they like clothing probably mean that they like to wear it. The skill that I learned as a patternmaker involves working in a very small, detailed world.
The details and lines on the inside of a piece of clothing require you to obsess over every last millimeter. Most engineers take a craftsman-like approach. I worked for more than a decade in this millimeter-level world, developing patterns and drawing lines. Different designers have different approaches, but there are some who want the clothing to be exactly as it is depicted in their design sketches. Once I started working with Miyamae-san, all of that changed.
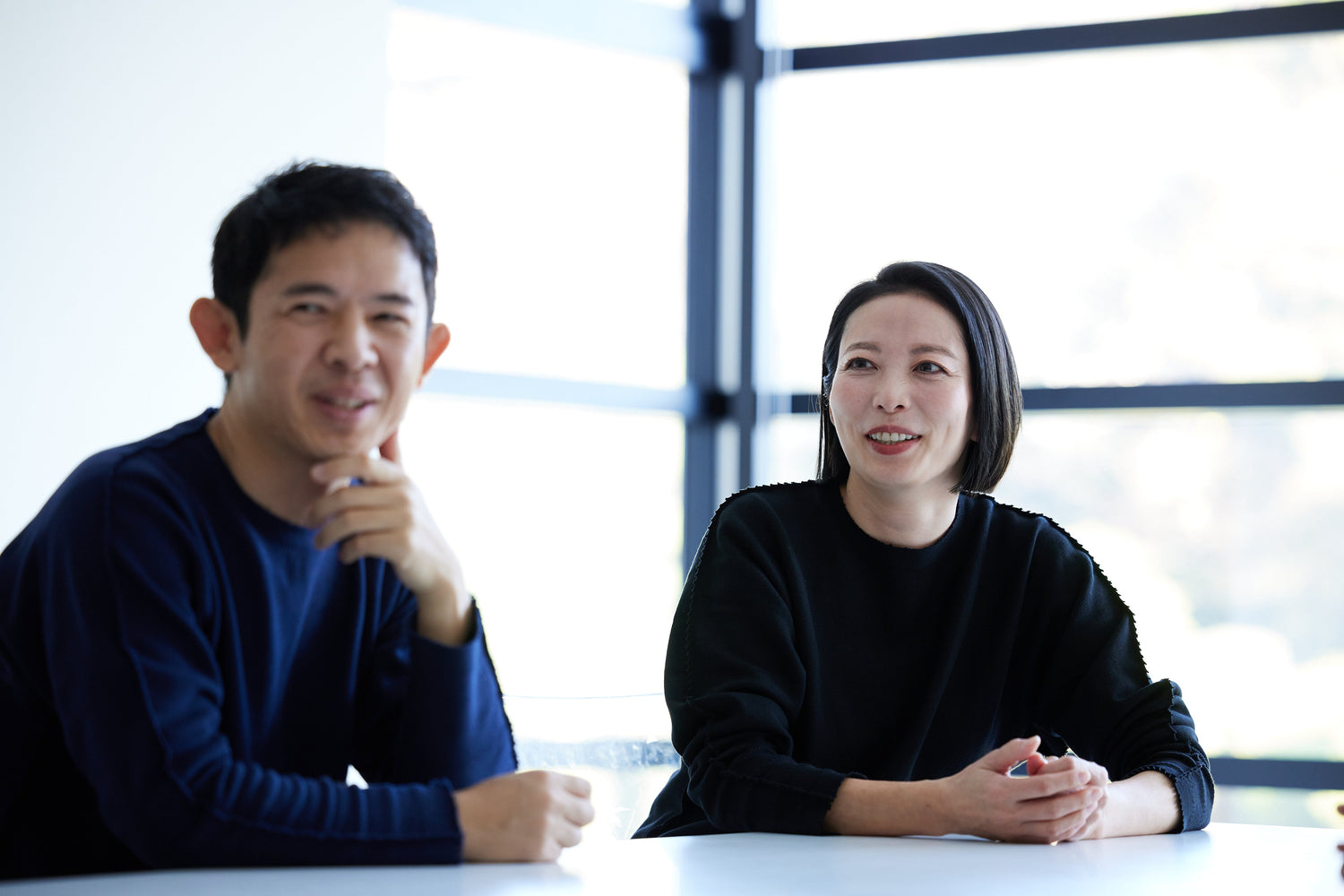
Miyamae: Designers all have their own approaches. There is one type that has a clear view of the world and wants to express it exactly as they imagined, but there is another type that wants to encounter worlds that have previously been unknown and unseen. I’m the latter. I’m not just interested in my own world, but I have always wanted to be surprised by what I create.
Obviously, this requires teamwork. A key part of being a designer is how you tap into the skills and capabilities of your team. Although it is sometimes necessary to develop sketches, the engineers at Issey Miyake are highly skilled, and once they have their sketches, they have the ability to create it exactly as depicted, or even better. But I don’t just want to validate the image that I have inside my head. Creation at Issey Miyake demands that you express things that no one has ever seen before. This is an extremely difficult hurdle, and it is crucial that you have a skilled team to meet those expectations.
The question is how you get a team to create something unknown, something that you cannot draw. The A-POC ABLE approach goes beyond just creating the final form and style of the clothing. We investigate completely new processes and the values and potentials for apparel that come out of them. When that is what you are trying to achieve, you’re often held back if your starting point is a completed, fully realized image and design drawing. That is why we use words, sketches and other methods to communicate ideas within the team and with people in other fields.
Takahashi: The design, fabrics and pattern all have to be in harmony or the clothing is no good. When you give a sketch to a patternmaker, what they worry about is finding the point where everything fits together. In this respect, A-POC ABLE offers an extremely simple and liberating approach. You start by considering what kind of clothing you want to create. Then, you investigate suitable materials and forms that work with those materials, and from there you move on to produce the patterns and design the fabric. The entire process moves forward very quickly.
- Hoshino, you just recently joined A-POC ABLE.
Takahiro Hoshino (“Hoshino” below): That’s correct. I joined the company in the planning unit and only recently moved to A-POC ABLE. I’m still learning about textiles and patterns. Up to this point, I was developing drawings and processing fabrics, but as I learned more about materials, I began to realize that I’d never really thought about how fabrics are made or how they change.
Even understanding just a small portion of that has opened up a wide range of new possibilities for me. Up until now, there has been a clear demarcation in my mind--I’ve always considered textiles and planning (design) to have separate roles. I’ve done a lot of work on how to process existing fabrics and how to give form to materials after they are processed, but I began to realize that there were limits to what I could achieve with just my own knowledge and experience.
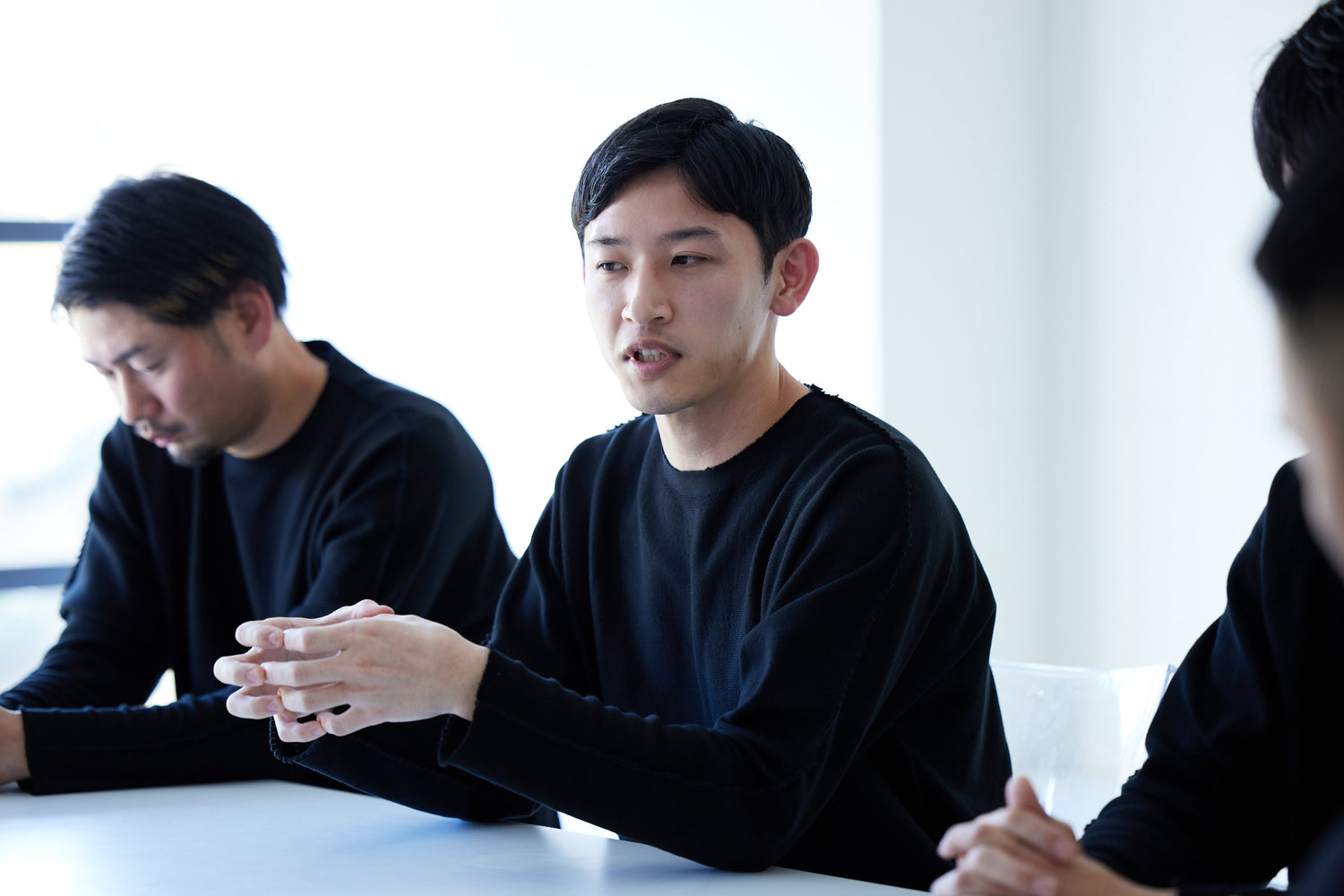
- What do you mean by limits?
Hoshino: What I mean is that if you use a certain material to design the form of a piece of clothing, you often encounter issues that you may not know how to solve. That’s because you really don’t understand the material, but if, for example, you begin to learn a little bit more about the thread, the knitting machines and looms, you begin to discover the intersection between those different ideas.
As one example, a weft knitting machine is very good for directly changing the texture and feel of a fabric simply by using a different kind of thread. Looms are able to create dense textures and new functions for the fabric by combining different kinds of thread and woven structures. That’s why it’s so important to understand the characteristics of both the materials and the machines. It is only when you understand the limitations of the machine and how to apply their unique characteristics that you are able to explore new materials that the world has never seen. What the machines that make thread and fabric do is actually very simple. But there are limitless possibilities once you begin combining them. What makes A-POC ABLE so interesting to me is that I am free to explore this.
- What is the benefit of creating teams of people who are engineers?
Miyamae: The first is that you can see the process of design and manufacturing from many different angles. Even the concept of “rethinking the manufacturing process” needs to be viewed from numerous perspectives, not just one.
People with Nakatani’s and Takahashi’s levels of experience already have many different perspectives just by themselves. But you need as many viewpoints as possible to make new discoveries and to gain new insights. That is one of the things we expect from new team members. They must have different levels and qualities of skill and experience, and that’s exactly what we want. In the creation space, hierarchy must be flat--you can’t have superiors and subordinates, everyone needs to bring their own perspectives to the table.
- So there are different expectations of different people?
Miyamae: For example, you may have a process that has become routine and commonplace to you, but a new member will ask why you do things in certain ways, could we not do something different. This casual approach and new viewpoint can be the inspiration for a fresh process. How someone contributes to the team will depend on how they question the way things are done and what makes them feel dissatisfied. Meanwhile, the team starts to be bound by fixed, immovable concepts if certain practices are taken as given and the way things have always been done.
That is what we expect from the team, and we use this process of communication to improve each other, which leads to growth for the team’s own design and manufacturing. Obviously, it’s important to have people who enjoy this kind of relationship, but I think that when there is conflict, or at least a difference of opinion, it stimulates ideas across the team.
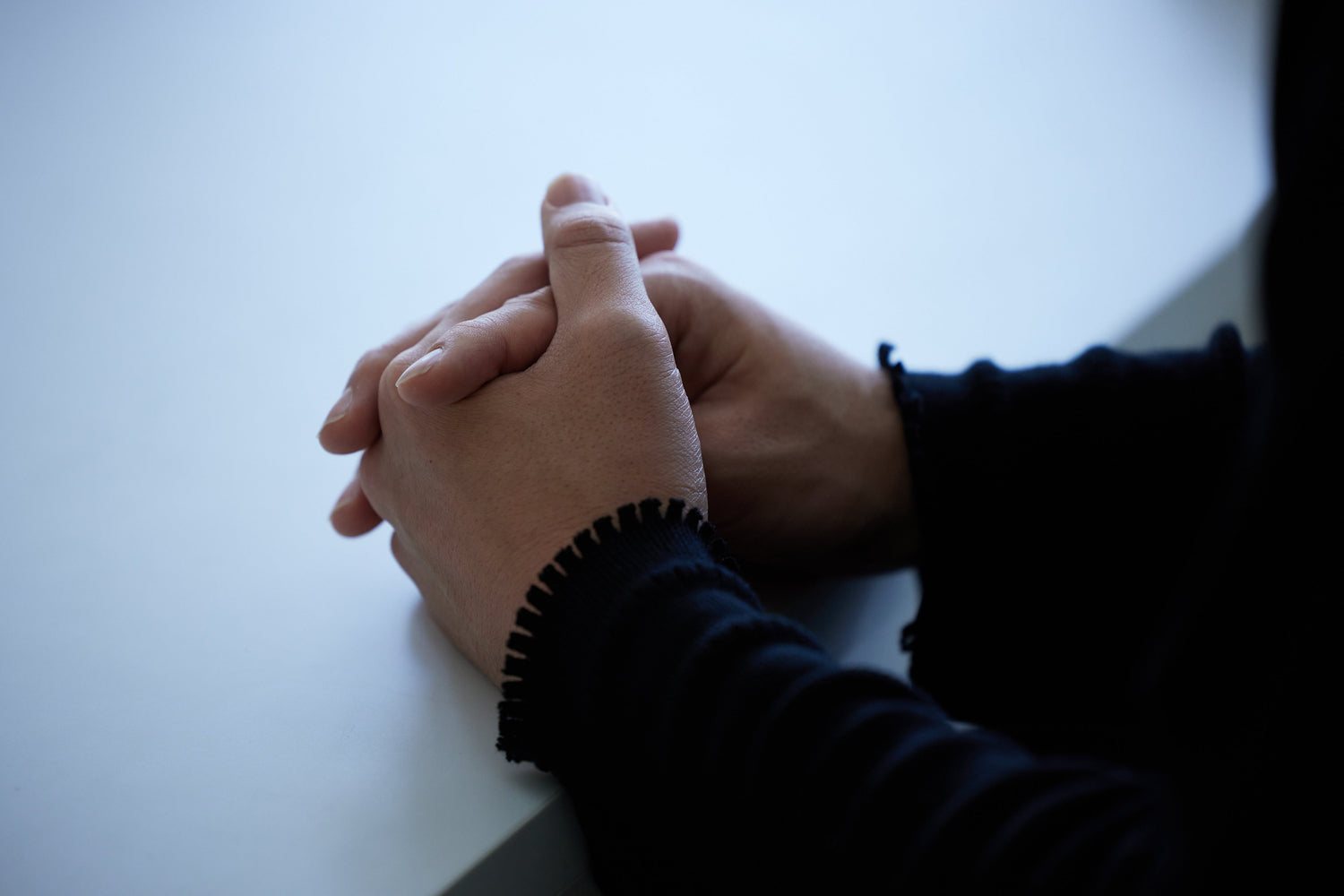
- Members themselves change, and this changes the work of the team.
Miyamae: When I was working on the Miyake side, this teamwork was what I found the most interesting. A large pendulum swing in perspective quickly changes your concepts and ideas. I think that’s one of the things that sets our teams apart from other maisons.
We sometimes consider what “Issey Miyake style,” means and for me, this goes beyond the superficial form and style of the clothing and is more about an expression of attitude and values in design and manufacturing. We continue to learn about design throughout our lives as we unfold Issey Miyake’s ideas.
One of the starting points for that is embodied in the phrase “A Piece of Cloth.” It is an extremely abstract concept, but that is exactly why you can continue to explore it. It’s philosophical, but it is also just interesting to be able to look into the essential nature of human beings and their apparel. When I am asked what “A-POC” means, I find it really hard to express the concept in words that will be readily understood by many people. When you are involved in manufacturing within the world of art and design, there is no single answer, and you may not be able to express your answers in language. That’s what makes it so interesting.
- What kinds of work do you spend the most time on in the Engineering Team?
Miyamae: We spend the most time on “preparing to design.” Before we ever start discussing the specifics of a design, each of us formulates our own “questions,” researches them, develops prototypes by hand, and creates materials and information that can be used in decision-making. We try to spend a lot of time and effort on this.
Takahashi: Basically, it feels like we are always “getting ready”. Throughout the year, we each make our own preparations, and then once every six months we hold presentations to share our ideas.
Miyamae: By regularly sharing ideas, the team can delve deeper into things they think have potential. If you don’t spend the time and effort on this kind of preparation, you are limited in what you can conceive and achieve. That is why one of the most important aspects of team management is providing individuals with the time to do their own research and work with their own hands.
- Do people talk with each other about what they are preparing?
Takahashi: Sometimes they do, sometimes they don’t. I think it’s a different approach from what an ordinary apparel company would probably use. It’s more like a research lab.
Miyamae: Individual experts want to have independent teams, so at A-POC ABLE we do not have seasonal themes. There is no reason to have a clearly delineated theme and unified view of the world every season. What we want instead is for people to dig as deeply as possible into what interests them. If there are areas where a team lacks skills or knowledge, we bring in outside experts or encourage collaboration among different fields and sectors, and I believe this is what allows us to continue to change and evolve.
- Have there been any organizations that served as references for the operation of the engineering team and their involvement in the creation process?
Miyamae: The early stages of A-POC led by Issey Miyake and Dai Fujiwara stand out. That period was foundational for me, and looking back, it was stimulating and fascinating. Of course, there was also tremendous pressure. While we had the freedom to conduct research, we had to discover something meaningful. You couldn’t just join without bringing something to the table.
It was truly liberating, but without knowledge and experience, you had to navigate through much trial and error. So, we couldn’t do everything at once; we had to progress step by step. Sometimes, we focused on exploring the world of dyeing or researching from the perspective of threads. Of course, there were times when our explorations led to dead ends, but the key was to keep moving forward because new discoveries wouldn’t happen otherwise.
- It’s more a form of training, isn’t it?
Miyamae: We felt that, as a company, Issey Miyake needed this kind of environment where people could concentrate on research and development. What we want to do at A-POC ABLE is develop platforms for the next generation. With A-POC and Reality Lab., Miyake continued to take on new challenges in manufacturing by creating new teams and environments which suited the changing times. Now it is our turn to create these kinds of opportunities, explore new possibilities and offer new innovations.
We have strong beliefs about certain things, but there is no saying whether what worked in the past will continue to do so. If you look back on it, Miyake came out with a new innovation in clothing design and manufacturing about once every 10 years, for example, pleats and A-POC. We began work about two years ago, and I am confident that if we continue to move steadily forward our team will produce new innovations.

- Through their individual research, our members accumulate experience and knowledge, and this changes what the team can accomplish and what processes it uses.
Miyamae: There are changes that we can’t even imagine that lie ahead of us, and that makes things very interesting. It’s intriguing when you don’t know what to expect. If design and manufacturing were only about what we can currently envision, it would be nothing more than a pre-established harmony, and that would be boring. Someone is always asking a new question, and this triggers an unexpected chemical reaction within the team. That, I think, is the value of the A-POC ABLE team.
Our mission is to look towards the future and develop mechanisms and environments that will enable us as an organization and a team to discover new possibilities. This requires people who are driven on their own by their individual questions of why. We need to think about how to ensure that people are able to work freely while still maintaining cohesion.
- I think the world is in a transition to non-centralized systems. In management, TEAL-style organizations began to be seen several years ago, and more recently, in technology, there is a focus on DAO (Decentralized Autonomous Organizations). I think the future of manufacturing lies within these larger trends.
Miyamae: And I think that will make it very interesting indeed. Or maybe it’s better to say that this team is engaged in a kind of experiment. Obviously, when we launched A-POC ABLE two years ago, we needed certain guidelines and mechanisms, elements that would comprise our brand, but as we go forward, I want to be able to develop more freely.
Even when you have an existing lineup of TYPE-A, B and C that continue on as universal products, you must constantly evolve. I want the team to continue to change and progress. I want each member of the Engineering Team to talk about their own ideas and concepts for design and manufacturing. Ideally, these team activities will attract people and win support for the A-POC ABLE brand. For this to happen, I think we as a team must be endlessly “curious” and “inquisitive,” endlessly excited by manufacturing.
- Curiosity and inquisitiveness may be the energy that drives manufacturing.
Miyamae: The question of “why” that Miyake kept asking us has become something of a mantra to encourage constant curiosity, inquisitiveness and ambition. New discoveries emerge out of questions. Apparel is something that you wear on the body, but it is also an opportunity to express your view to society at large. What I mean is that you can expand and contract your perspective, telescope between the body and the society you live in. Miyake took a big-picture view of the world, bringing boundless creativity and wide-ranging perspectives to his apparel. He would often tell us, “Use clothing design to truly see the world.” Our curiosity and inquisitiveness are what enable us to take on that challenge. It may seem never-ending, but it is an extremely enjoyable task. That is the kind of platform I want A-POC ABLE to become.
Stay tuned for Episode 1, where we will be discussing “What Is Engineering?”.